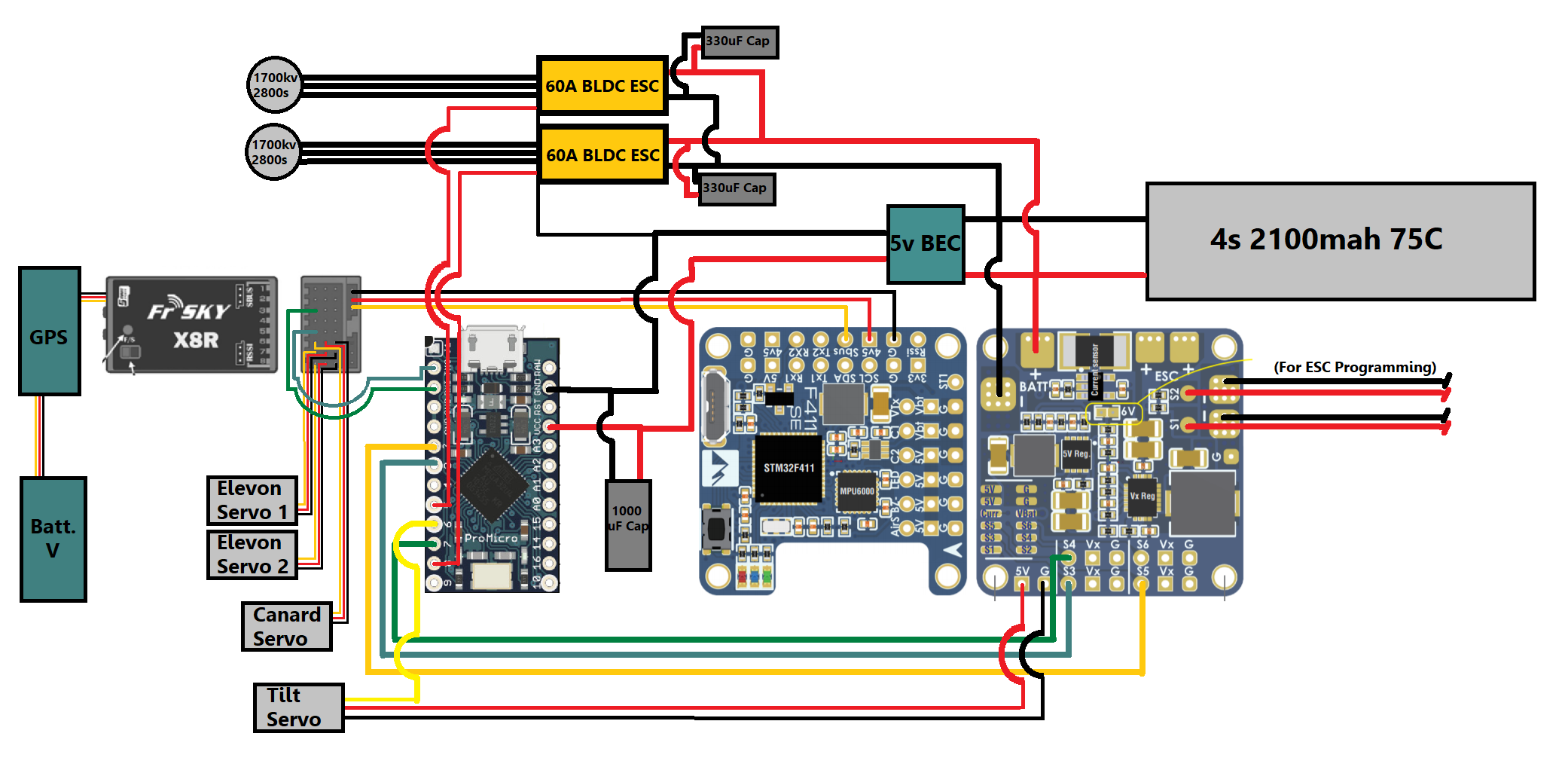
Embedded/Controls
Novel multirotor designs, Closed Loop control analysis, Simulink, PX4, C programming, STM32-based microcontrollers
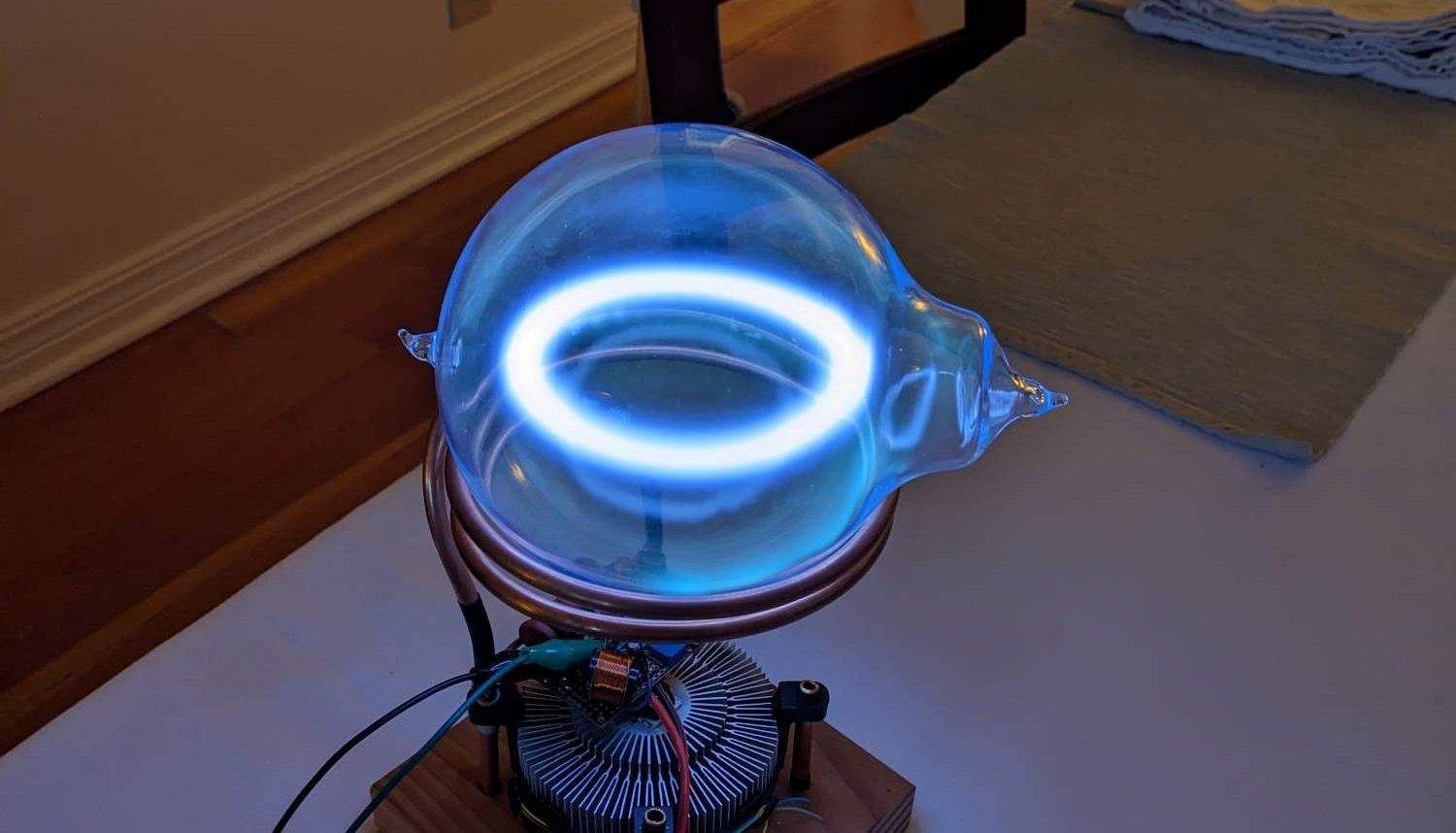
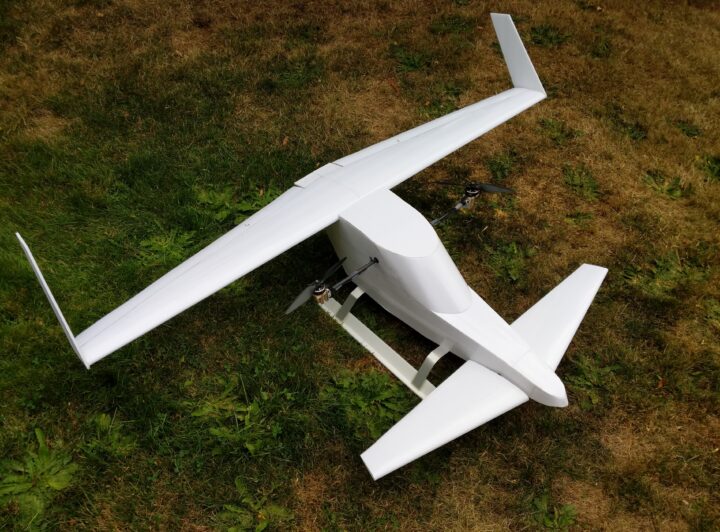
RC Aircraft
A longstanding obsession with making things fly. From a functioning eVTOL concept, to Solar gliders and more. Solidworks, Athena Vortex Lattice